World Heritage-listed Lord Howe Island — just 11km long, averaging about 2km wide — is enacting not only current wastewater, green energy and island-wide clean-up and pest eradication initiatives, but is also hoping to re-introduce flora and fauna that has been absent from its shores for generations.
The island lies about 400 miles offshore from the Australian State of New South Wales and is administered by its own statutory authority, the Lord Howe Island Board. With a population of about 400 and a limit to the same number of tourists on the island at any one time, it is located in the Tasman Sea region of the South Pacific Ocean.
In recent years, residents of the island began an environmentalist campaign. It aims to remove all invasive or unwanted species, use solar power to provide two-thirds of the community’s annual energy needs, and gain EPA approval to reuse the solids from treated sewage effluent produced by the island’s environmentally sensitive, low-energy wastewater treatment plant as compost.
The plant is part of an upgrade of the sewerage management system on the island, where there are about 220 septic tank systems — 25 of which are connected to commercial operations. Previously, sludge from the tanks was collected and spread on drying beds to dewater. The process was smelly, involved much handling, and could take extended periods of time to complete, particularly if the weather was not ideal for drying.
A new solid-liquid separation system from Kendensha Co. (KDS) has been installed by the Australian and Asia-Pacific wastewater treatment specialist CST Wastewater Solutions (CST) as part of a broader wastewater treatment system. The system uses durable, low-maintenance liquid-solid separators which produce light, clean, and readily handled output.
Sludge from septic tank pump-outs is delivered to the new waste treatment facility through a 1,800 liter wastewater tanker. The effluent travels through both coarse and fine screens, and is then pumped to a polymer dosing tank. A spreadsheet helps set the polymer dose and predicts the amount of liquid and biosolids that will be produced. These predictions allow for better planning for reuse of the final products.
The drier output is more compact and easier to convert to a valuable reuse product compared with the heavy, sloppy, and smelly product produced in the past, which was difficult to handle and dispose of. The old system required the solids to be dug out of the evaporating bays, which produced strong odors. The new system occupies a smaller footprint, produces minimal odor and requires less on-site maintenance.
The pre-treatment and recovery technologies now produce clean liquid waste and dry, reusable solid waste that is easy to recycle.
Selection Process
CST was tasked to review a best fit sludge dewatering system for the septic waste, because the old infrastructure was becoming outdated and the existing drying beds were to be decommissioned. The company’s team worked extensively with the Lord Howe Island Board to find an optimal solution that combined environmental performance with an equally strong occupational health and safety performance — and which has a much smaller footprint than the drying rack system used previously.
“Our benefits to date will be extended further if EPA approval is received to incorporate the compacted solids from the effluent into compost for use on the island, incorporating previously odorous waste into a valuable resource and further reducing the need for transport and landfill,” said Lord Howe Waste Management Facility Supervisor Bradley Josephs.
The waste management facility can now handle greater volumes of effluent for the Island. The solid waste is mixed with other diverse waste streams that are sorted, mixed, and prepared for re-use through an in-tunnel composting system. Waste treated in this way includes food waste, paper and cardboard, green waste, and grease trap wastes.
“We have witnessed a strong range of benefits since installing the system; the drier biosolids, for example, can now be stored in smaller 50L tubs which are far more manageable,” said Josephs. “The polymer dosage used in the new process is able to chemically remove suspended solids from the solution at a better rate than evaporation. This means that the liquid waste that is produced is much easier to treat via aerobic digestion.”
The precise polymer dosage process also allows the supervisor to know how much time the plant will take to produce particular quantities of processed solids.
“Drying used to be something of a guessing game, with the drying beds and reed beds we used. It would vary with weather, with humidity, and many factors,” continued Josephs. “But now the liquid-solid separation is beautiful, swift, predictable, and precise. This speeds up the process and enables us to tailor output for ongoing processing without waste storage issues.”
Waste liquid separated out by the CST system is processed via aerobic digestion, while the solids component is dewatered through the KDS separator and then incorporated into a feed for the composting unit. This composting unit produces a fine, dried output that could soon be used for composting by the island’s residents.
“Due to the nature of the in-vessel composting unit on island, dried biosolids can be processed and used to create useful compost that will be available to the public,” said Josephs. “The biosolids are currently mixed with food waste, paper and wood chips at a ratio of 0.05/1/2/1 per day. Once we have more results in regard to compost composition, we aim to be able to create an optimum ratio of biosolids used in the procedure to produce compost and further reduce our environmental footprint.”
Community Support
These environmental and waste initiatives enjoy the support of the island’s residents, tourists, and local businesses.
The CST screening, dewatering and compacting component of the WWTP system is more economical, more compact in terms of site use, and uses less energy than before. It accords well with the island’s environmental, waste, water, and energy conservation objectives, said David Waterhouse, manager for infrastructure and engineering services with the Lord Howe Island board.
The island is also actively working toward permission to use the system’s output as compost, through a Resource Recovery Exemption. If the island gains permission, the compost could easily be used to help re-grow the native flora that has been missing for generations — an initiative that’s heavily supported by the island’s citizens. WW
Published in WaterWorld magazine, February 2022.
About the Author
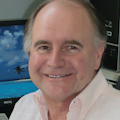
Michael Bambridge
Michael Bambridge is managing director of CST Wastewater Solutions. He is an industry authority on sustainable wastewater, water recycling and waste-to-energy engineering. A chemical engineer who values quality and enduring solutions over quick fixes and one-size-fits all, his experience of major municipal and industrial projects extends over more than 30 years throughout Australasia and the Asia-Pacific, regions where clean water shortages are endemic and avoidance of groundwater contamination is paramount.