Safeguarding the water supply: Breathing new life into Daytona Beach's treatment plant
The Ralph Brennan Water Treatment Plant — serving more than 100,000 Daytona Beach residents and Volusia County businesses — faced a pressing challenge: maintaining uninterrupted service while undergoing a $6.6 million upgrade. Processing up to 24 million gallons of water per day (MGD), its operation is vital to the central Florida community and its status as a global tourist destination.
“This plant is the final stop before water reaches customers,” said Eric Smith, P.E., Deputy Utilities Director of Daytona Beach. “In every decision in upgrading our plant, we needed to account for public safety, ensure continuous service and directly support clean water for our community.”
Intended to extend the facility’s service life by an estimated 20 to 30 years, the project addressed decades of wear and tear on concrete filter cells, coating systems and other critical infrastructure. In addition to restoring essential systems, the effort aimed to bolster the plant’s long-term capacity.
This ambitious 18-month undertaking marked Daytona Beach’s first use of a design-build delivery model, integrating design and construction under one team. The upgrades included repairing concrete, applying new coatings, replacing underdrains and valves and integrating modern control systems.
“We needed a flexible approach to deal with all the unknowns,” said Smith. “For instance, each basin presented surprises once it was drained — no two were the same.”
A balancing act: Upgrades without interruption
At the heart of the project was the restoration of six gravity filter basins (Figure 1), each with unique conditions, including deteriorated concrete. The coatings also varied from thick epoxy layers — up to 125 mils — dating back 50 years, to thinner applications from the early 2000s.
The decision to rehabilitate rather than replace the infrastructure called for creative solutions and advanced technology to minimize environmental impact while keeping the plant running.
Older filters, operating at reduced capacity — around 3 MGD instead of the design parameter of 5 MGD — left no redundancy during the project. To maintain daily capacity, five basins had to remain online, allowing only one to be taken offline at a time for refurbishment. This required careful coordination among engineers, contractors and plant operators, as each filter cell — varying in age and condition — was individually taken offline and restored to ensure continuous plant operation despite capacity constraints.
“Every step, from upgrading the filtration system to surface prep to final coatings, was designed to minimize downtime and make sure the plant maintained its required capacity,” said Todd Newman of Exceletech Coating and Applications LLC — a Central Florida-based applicator of industrial and commercial coatings and high-performance linings — that worked with general contractor PC Construction. “It was a delicate balance of precision, planning and teamwork.”
The project required more than 45 individual shutdowns, necessitating precise coordination between the project’s collaborators.
Chip off the old basin
Removal of the old, thick epoxy layers was particularly demanding in the older basins.
Crews used saw-cutting keyway lines, pneumatic chipping and scraping to strip coatings down to the bare concrete. Surface prep for these basins involved abrasive blasting with coal slag to achieve a concrete surface profile (CSP) of 8-9, followed by 5,000-psi pressure washing to eliminate debris and prepare for resurfacing (Figure 2).
For areas with significant substrate damage (Figure 3), crews employed vertical mortars and cementitious resurfacing materials to restore the original profile.
In the newer basins, where coatings were thinner — about 20 to 30 mils — less aggressive methods sufficed. Surface grinding smoothed high areas, while rapid-cure vertical mortars patched exposed rebar and deeper damage (Figure 4). Applicators applied Sherwin-Williams Dura-Plate 2300, a cementitious resurfacing material, by hand to an average thickness of 3/16 inch, creating a robust foundation for the new coatings (Figure 5).
“This project was about giving fresh life to old infrastructure,” said Smith. “You can’t just rip out and replace concrete — the investment lies in extending its life with the proper coating systems.”
Final coatings included multiple layers of Macropoxy 5500, applied to reach a thickness of approximately 20 mils dry film thickness (DFT) (Figure 6). For moisture-prone concrete surfaces, crews selected Pro Industrial, a catalyzed water-based epoxy chosen for its moisture resistance and breathability. Applied using an airless spray and back-rolling technique, this system provides uniform protection against contaminants.
Each basin took around three weeks to bring back into service (Figure 7), including performing meticulous surface preparation, applying coating materials and installing mechanical equipment and filtration media. The team also performed rigorous holiday testing using high-voltage equipment to detect even the smallest coating flaws.
Water treatment staff and city officials provided ongoing oversight, coordinating shutdowns and ensuring project milestones were met. The Florida Department of Health in Volusia County closely monitored the project, requiring disinfection and clearance inspections for each refurbished cell.
Precision and protection in the pipe gallery
The water treatment plant rehab also included significant upgrades to the facility’s pipe gallery (Figure 8), where extensive corrosion had compromised equipment. Crews used a 5,000-psi rotator tip pressure wash and electric bristle blasters to address corroded areas without damaging nearby sensitive instrumentation.
Corroded areas were spot-primed with Macropoxy 920, followed by two coats of Macropoxy 646 and a final layer of Acrolon 218. Stainless steel hardware replaced older, corroded components.
Environmental and safety considerations were also central to the project. Custom-built containment structures surrounded each basin (Figure 9), as well as ancillary pipes and equipment, to prevent contamination, and were inspected daily for compliance.
“This project exemplifies how collaboration between contractors, applicators and manufacturers can overcome complex challenges while keeping critical infrastructure operational,” Newman said.
For particularly sensitive areas of the treatment plant, shrink-wrap barriers and drop cloths were used, and dehumidification systems provided stable climates that were needed for optimal coating adhesion.
“The entire project team understood that this isn’t just maintenance,” said Smith, “it’s an investment in reliability through the right work and the right products.”
Future-proofing a community’s water supply
The upgrades have equipped the Ralph Brennan Water Treatment Plant to reliably serve Daytona Beach’s growing population for decades to come. With systems expected to perform for up to 30 years, the project should exceed all prior service intervals.
“Every decision, from material selection to scheduling, was made with one goal in mind: delivering long-term value to the community,” Smith said.
The project’s phased approach, attention to detail and focus on durability have not only restored critical systems but have also provided a blueprint for future water infrastructure projects. In fact, the collaborative approach taken by the city and project team earned them runner-up status in the 2023 Sherwin-Williams Impact Award program, a testament to the project’s innovative solutions and careful execution.
As Daytona Beach looks to the future, the Ralph Brennan Water Treatment Plant is poised to provide safe and reliable water for years to come — to residents and tourists alike.
“It’s been more than a generation since we tackled anything like this,” Smith said. “Ideally, the work we’ve done means I’ll be retired before it needs to be addressed again.”
About the Author
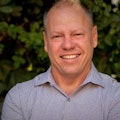
Paul Trautman
Paul Trautman has more than 30 years of experience in the paints and coatings industry working in various capacities, including more than 20 years with Sherwin-Williams Protective & Marine, where he is currently Market Director of the Water Infrastructure segment. Trautman has authored technical papers related to protective coatings and presented educational programs for the Society of Protective Coatings (SSPC) Coatings+ Conference and regularly hosts educational luncheons for municipalities, industrial facility owners and consulting engineering firms.
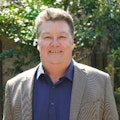
Kevin Ayers
Kevin Ayers has 32 years of experience in the paints and coatings industry, with 20 years dedicated to Sherwin-Williams Protective & Marine. Currently serving as Asset Protection Manager – Water Infrastructure, Ayers spent 15 years as a multi-segment representative on Florida’s East Coast, specializing in wastewater treatment (WWT) for the past five years. His expertise spans both sales and business development within the WWT sector. Highly credentialed, Ayers holds NACE Level 3 / AMPP Senior Certified Coating Inspector and AMPP Concrete Coating Inspector Level 2 certifications.